
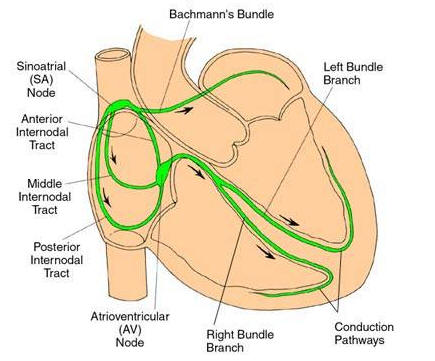
Therefore, in the presence of electrical excitation they effectively convert a pressure or weight to an electrical signal.
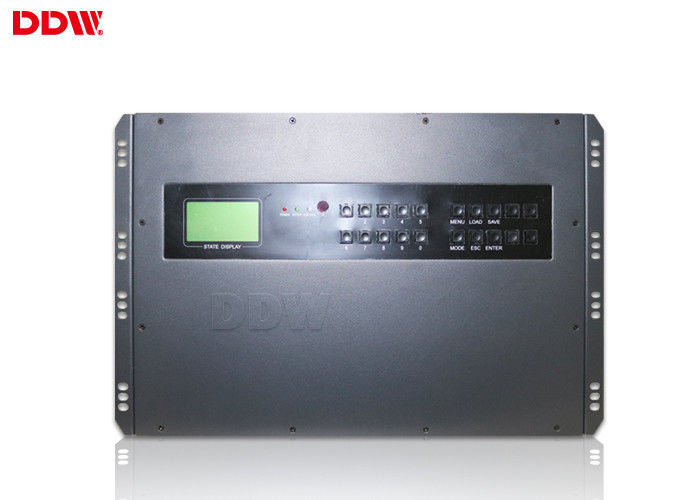
In principle, all strain gauges react to an applied force by varying a resistance value. Compared to metal-foil-type transducers, piezoresistive transducers are more sensitive with better linearity, but have large temperature dependence and large initial offsets. The two most common types of strain gauges are the metal-foil type used in a variety of weight/pressure sensors, and the semiconductor-based peizoresistive transducers, widely used to measure pressure. Each application has its own diverse needs for precision, accuracy, and cost.Īlthough there are several methods and technologies for measuring pressure and weight (force sensing), the most commonly used measurement element is the strain gauge. The applications for force sensors are vast and range from vacuum gauges, to heavy machinery weigh scales, industrial hydraulic equipment, and manifold absolute pressure (MAP) sensors for internal-combustion engines. Pressure- and weight-measurement devices can be regarded as "force sensors," since force is the property that affects the transducers' outputs. Pressure measurement is especially important, as it is also used indirectly to measure flow, altitude, and other properties. The need to detect and measure pressure and weight is a very common requirement for modern industrial control and system monitoring. Pressure Sensors and Weigh Scales (Force Sensing) Overview Example circuits and block diagrams help the reader select an optimal set of parts to meet their design needs. The article introduces the intricacies of selecting a signal path. This tutorial explains the sensor signal chain for the most popular sensor transducer types for pressure, temperature, current, light, and proximity sensing.
